Utility Our utility building system has been developed to be used in both large and small spaces
VDL De Meeuw has built an impressive logistics hub to optimise construction and renovation projects at Schiphol Airport.
This hub, which covers about 130,000 square metres south of the airport, offers space to accommodate people, equipment, vehicles and construction materials. This site will enable Schiphol to effectively implement its future plans. As part of this project, VDL De Meeuw completed four main buildings: three office buildings and a porter’s cabin with a training area.
Schiphol
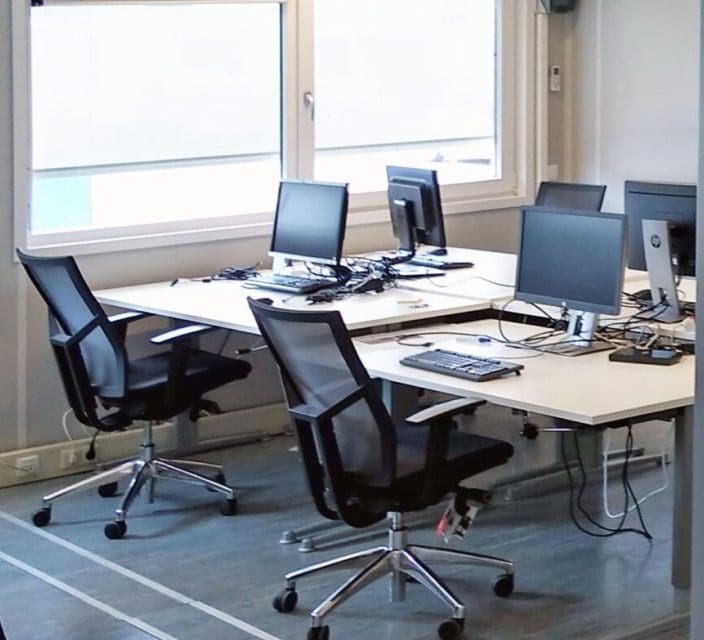
Strict timeline and noise reduction measures
The biggest challenge in this project was the strict (noise) requirements and the tight time schedule. Katrien van Eijck, Account Manager at VDL De Meeuw, explains: “We delivered the first two buildings within a month. The other two buildings followed 14 days later.” Noise reduction measures were crucial because of the low-flying aircraft. The requirements could be met by installing attenuated ventilators and other sound insulation measures. “After submitting the initial request, a quote was sent within four days. And three weeks later the first building was installed,” Katrien said.
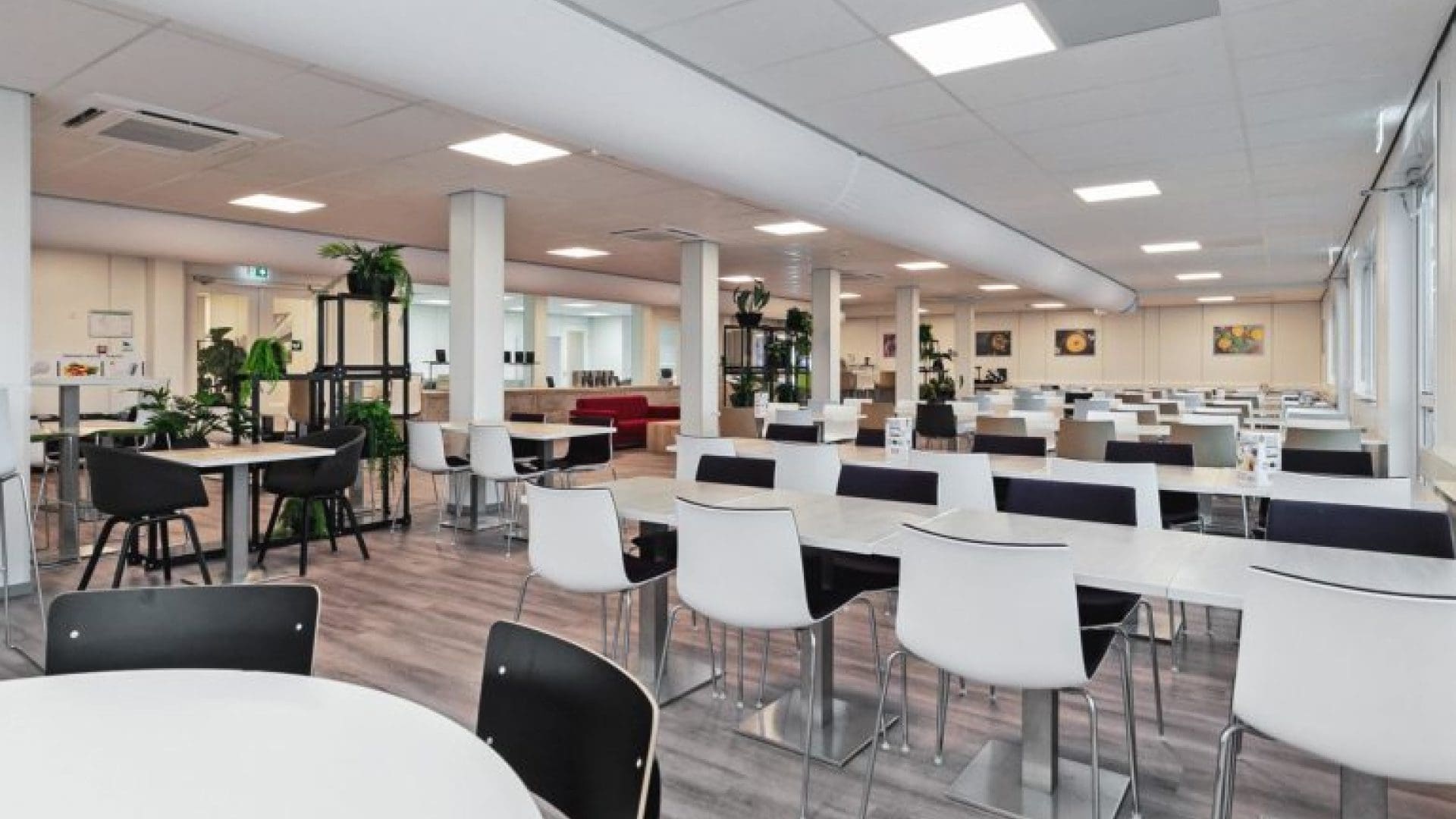
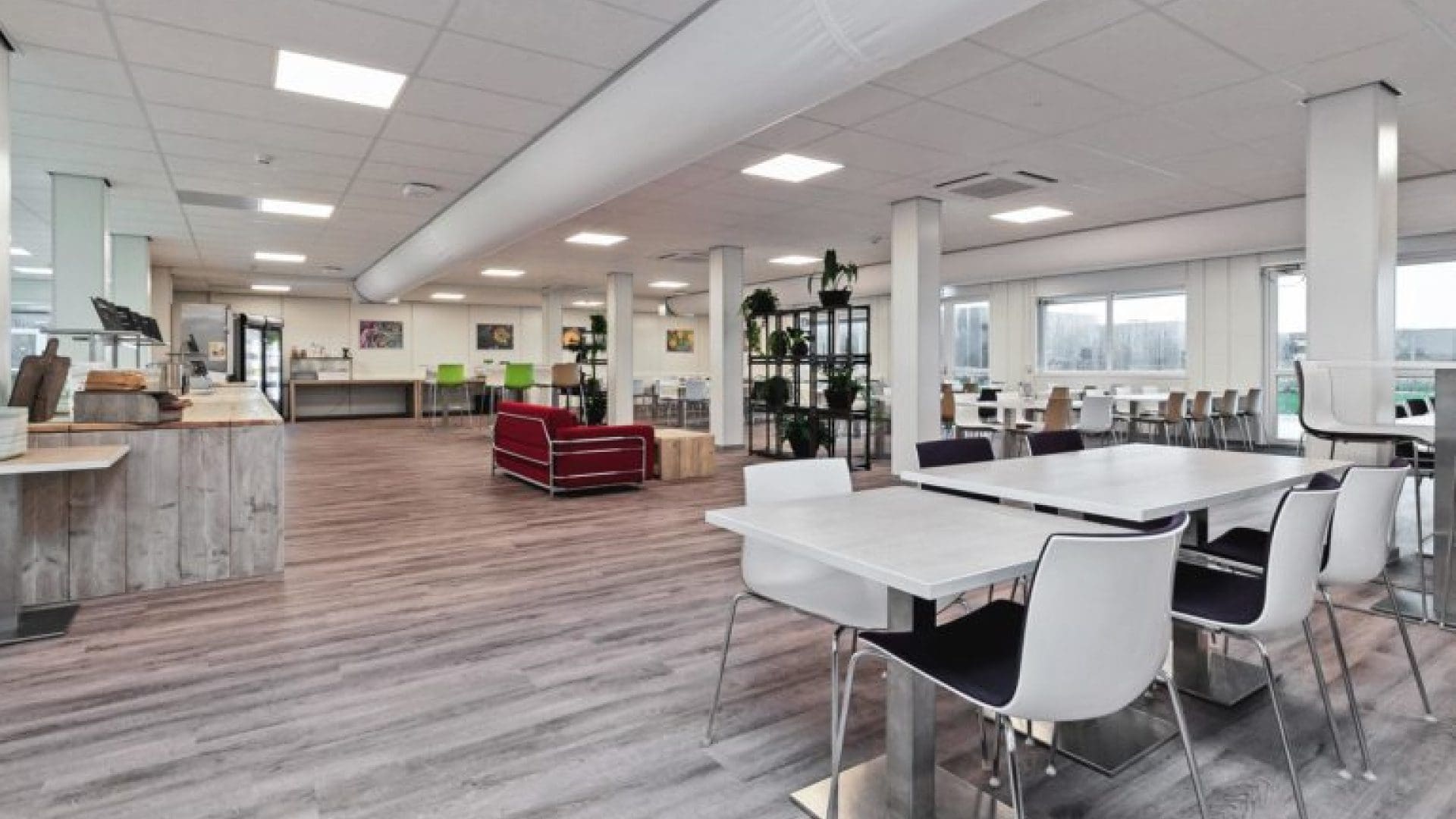
Extension including a canteen and meeting room
To expand the logistics hub, VDL De Meeuw also designed, installed and delivered a large canteen within four months. This building, covering an area of 527 square metres, can accommodate 200 people and features a high-quality finish with PVC flooring. The all-glass meeting room creates a sense of openness and transparency.
“We have found working with VDL De Meeuw to be a very pleasant experience; the company is flexible. They are proactive and keep a close eye on the whole process.”
Tom Bekker, Partner at DVP
Comfort and safety
The installations in the canteen are designed to provide users with all the comfort they need. The building is heated and cooled via a VRF system and features mechanical ventilation. To prevent noise pollution from the nearby runways, special soundproofing measures have been taken, such as a suspended spring ceilings, extra sealant for gaps and attenuated ventilators. The building is also equipped with an intrusion alarm, a fire alarm and an evacuation system, all contributing to increased security.
Stringent safety requirements and procedures
Strict safety procedures had to be followed during construction to ensure the safety of both people and aircraft. Despite these challenges, VDL De Meeuw managed to meet the tight four-month schedule without any compromise on quality.
This comprehensive project demonstrates just how flexibly and efficiently VDL De Meeuw can work. And with its eye for detail and safety, it has made a positive contribution to Schiphol’s plans for the future.
From the outside, there is little difference between modular buildings and traditional structures. In fact, it is actually impossible to distinguish between the appearance of modular flexible housing and traditional real estate. More and more architects are approaching VDL De Meeuw about flexible housing developments. Flexible housing and traditional real estate have to comply with the same requirements. In other words, both comply with the Dutch Environment Buildings Decree (Bbl).
The modules that come together to form the final building are produced in a controlled environment. This ensures a safe working environment with a high level of control over quality and minimal impact on the production process due to weather. This in turn prevents delays and failure costs, and increases control over the overall project. Speed and quality go hand in hand here.
After production, the modules are transported to the site. Once on site, these modules are connected to each other, to the electricity grid, to the sewerage, and so on, and the interior is finished according to the specifications agreed upon. At that point, the building is then commissioned and modified in the future according to any changing requirements.
Brochure
Flexible housing, always the space you need
Download the brochure here.
"*" indicates required fields
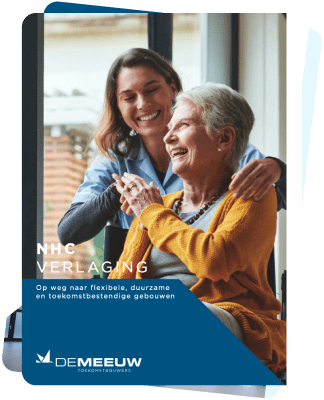