Utility Our utility building system has been developed to be used in both large and small spaces
Not only has this school grown in terms of dimensions, but it has even been relocated
Hyperion Lyceum, located in the Overhoeks neighbourhood close to the Amsterdam EYE, is one example of the possibilities De Meeuw offers schools.
A school that grows with its pupils
In 2011, Amsterdam schools association, VOvA received approval to build temporary accommodation for 175 pupils at Hyperion Lyceum. On behalf of ROC Amsterdam, in 2012, Phase 1 of Hyperion Lyceum was delivered by De Meeuw, in collaboration with the VOvA and Burton Hamfelt Architectuur Stedebouw Prototypes.
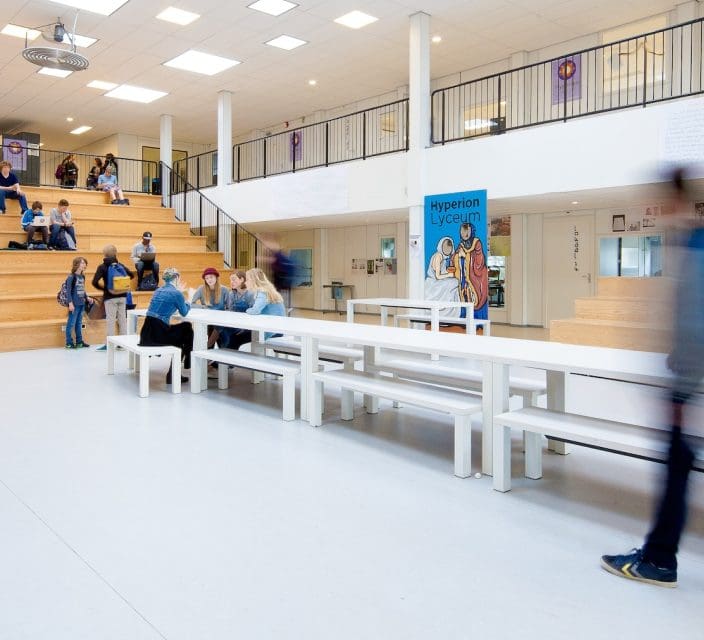
Family feel
The building’s features include an entrance with large balcony, hall with staggered skylights and a striking stairwell. The specially-proportioned window frames are a prime example of flexibility in this build, having been custom-made for Hyperion. The building is conducive to meeting-up and connecting. Small-scale, light, safety, transparency, colour and ambiance were the core values behind the design, which promotes connectivity, encounters and a family feel. The large wooden steps – which double up as seats – are at the heart of the school and represent a lounge area where pupils can meet.
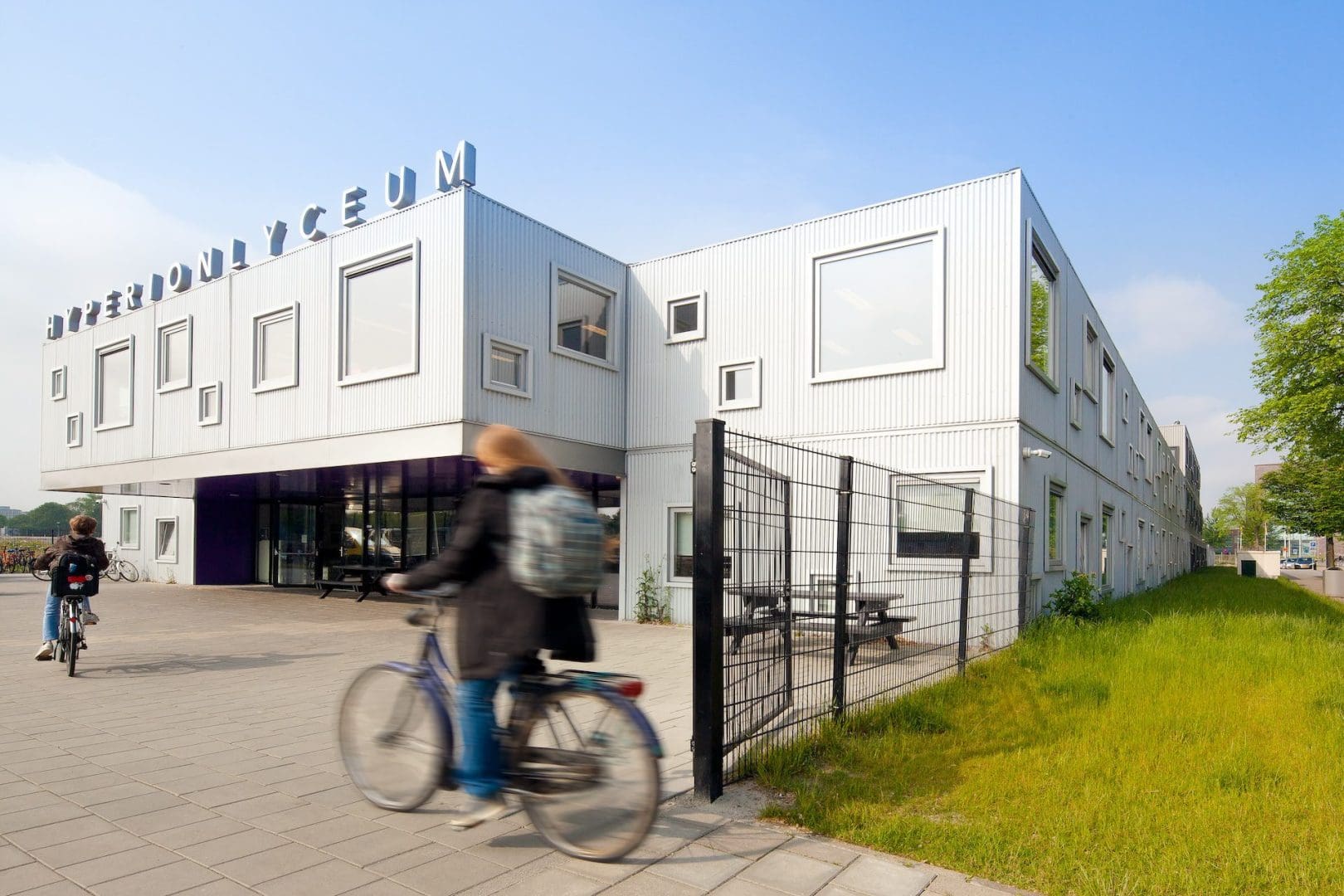
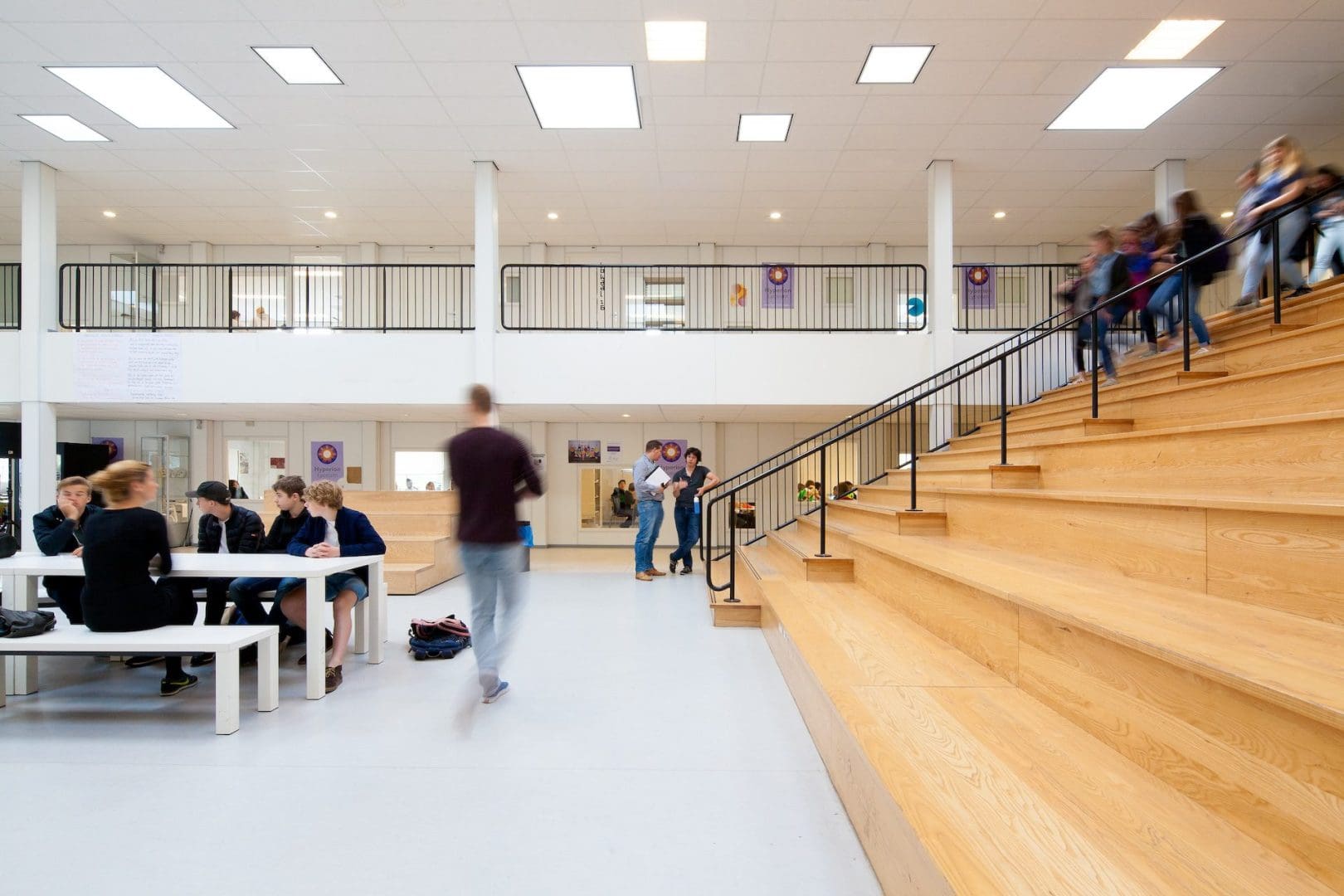
Relocation and expansion
Hyperion Lyceum temporarily moved to number 10 on the Tolhuisweg in Overhoeks in September 2011. Building developments in the area meant that the school had to be relocated. De Meeuw’s modular building system provided the perfect solution, and so Hyperion Lyceum was moved in mid-2015. In addition to the relocation, the building also underwent changes to its structure as a result of the merging of multiple phases.
A project on a tight schedule
It was clear from the start that this was a huge operation. De Meeuw succeeded in realising this complex dismantling, relocation and expansion project. This was done within the only time frame available that would not disrupt lessons: the six-week school holiday. Watch the video below to see how it was done.
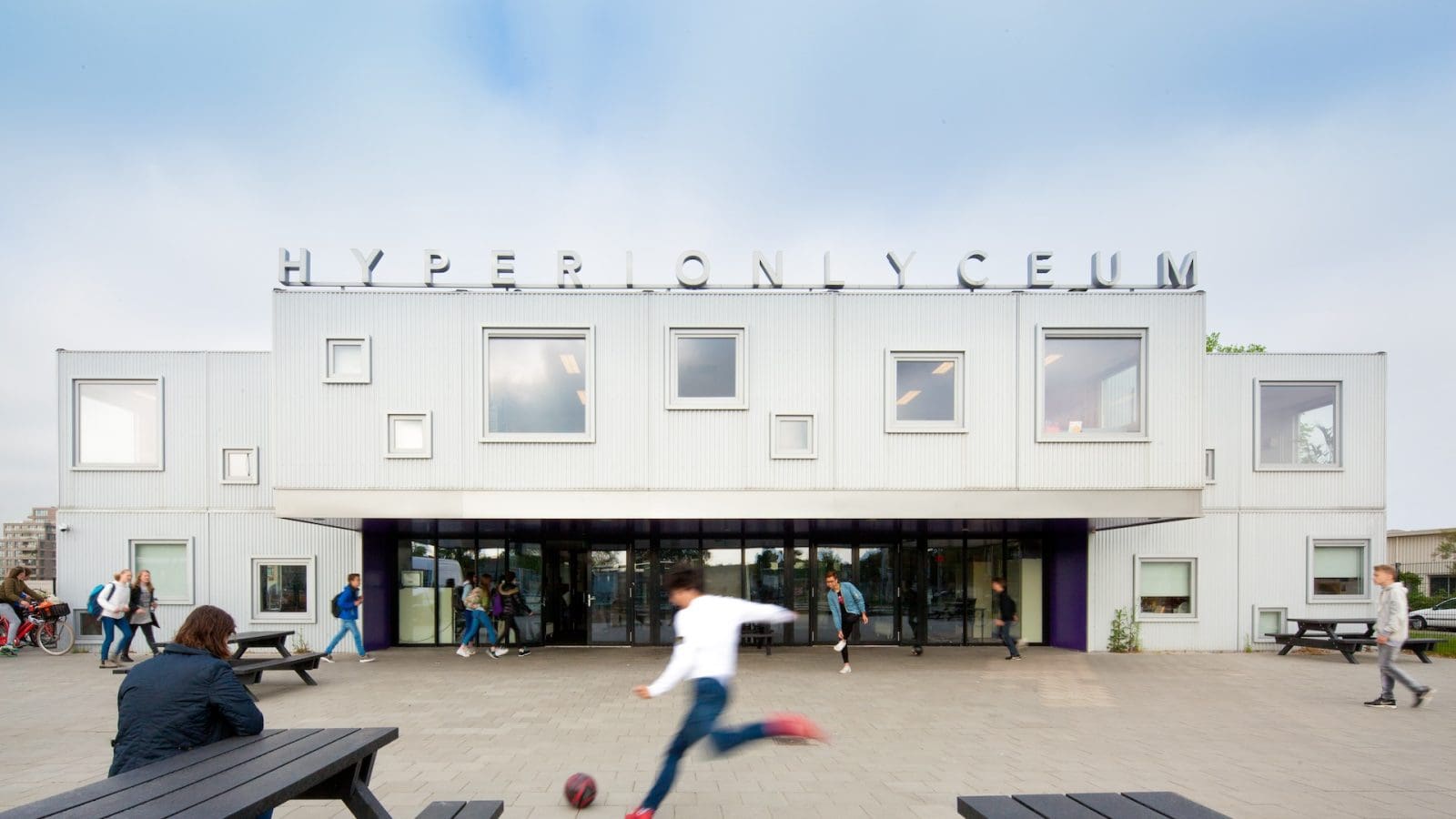
From the outside, there is little difference between modular buildings and traditional structures. In fact, it is actually impossible to distinguish between the appearance of modular flexible housing and traditional real estate. More and more architects are approaching VDL De Meeuw about flexible housing developments. Flexible housing and traditional real estate have to comply with the same requirements. In other words, both comply with the Dutch Environment Buildings Decree (Bbl).
The modules that come together to form the final building are produced in a controlled environment. This ensures a safe working environment with a high level of control over quality and minimal impact on the production process due to weather. This in turn prevents delays and failure costs, and increases control over the overall project. Speed and quality go hand in hand here.
After production, the modules are transported to the site. Once on site, these modules are connected to each other, to the electricity grid, to the sewerage, and so on, and the interior is finished according to the specifications agreed upon. At that point, the building is then commissioned and modified in the future according to any changing requirements.
Brochure
Flexible housing, always the space you need
Download the brochure here.
"*" indicates required fields
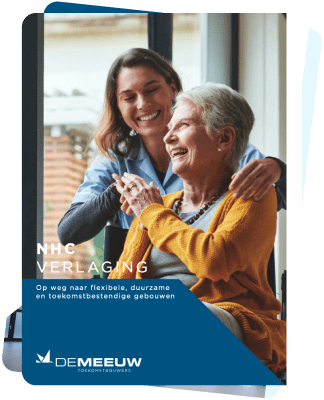