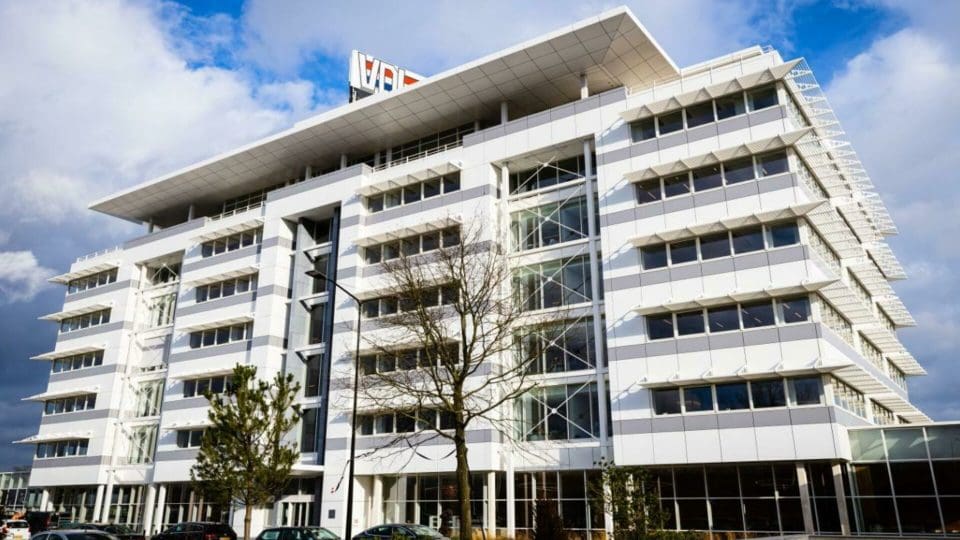
Productivity in the construction sector needs to be stepped up in order to meet the huge demand for housing in the Netherlands. VDL De Meeuw is of the opinion that a building should be viewed as a product rather than a project. “In our newly refurbished factory in Oirschot, we can build 500 residential units. That’s a good start. We have plans to scale up in similar batches to a production rate of 2,500 units per year,” states Operations Director Bram van Rijt.
One hallmark of the construction industry is customisation, notes Joziene van de Linde, Managing Director of VDL De Meeuw. “It is still often the case that clients talk more about what a property should look like rather than what requirements it has to meet. When you buy a car, you also don’t mention what kind of steering wheel to install. But that’s what we do in construction. There is a misconception in the market that buildings are going to be ugly and boring. But if you listen carefully to your customers and understand their requirements, you can also build very attractive buildings on a product level.”
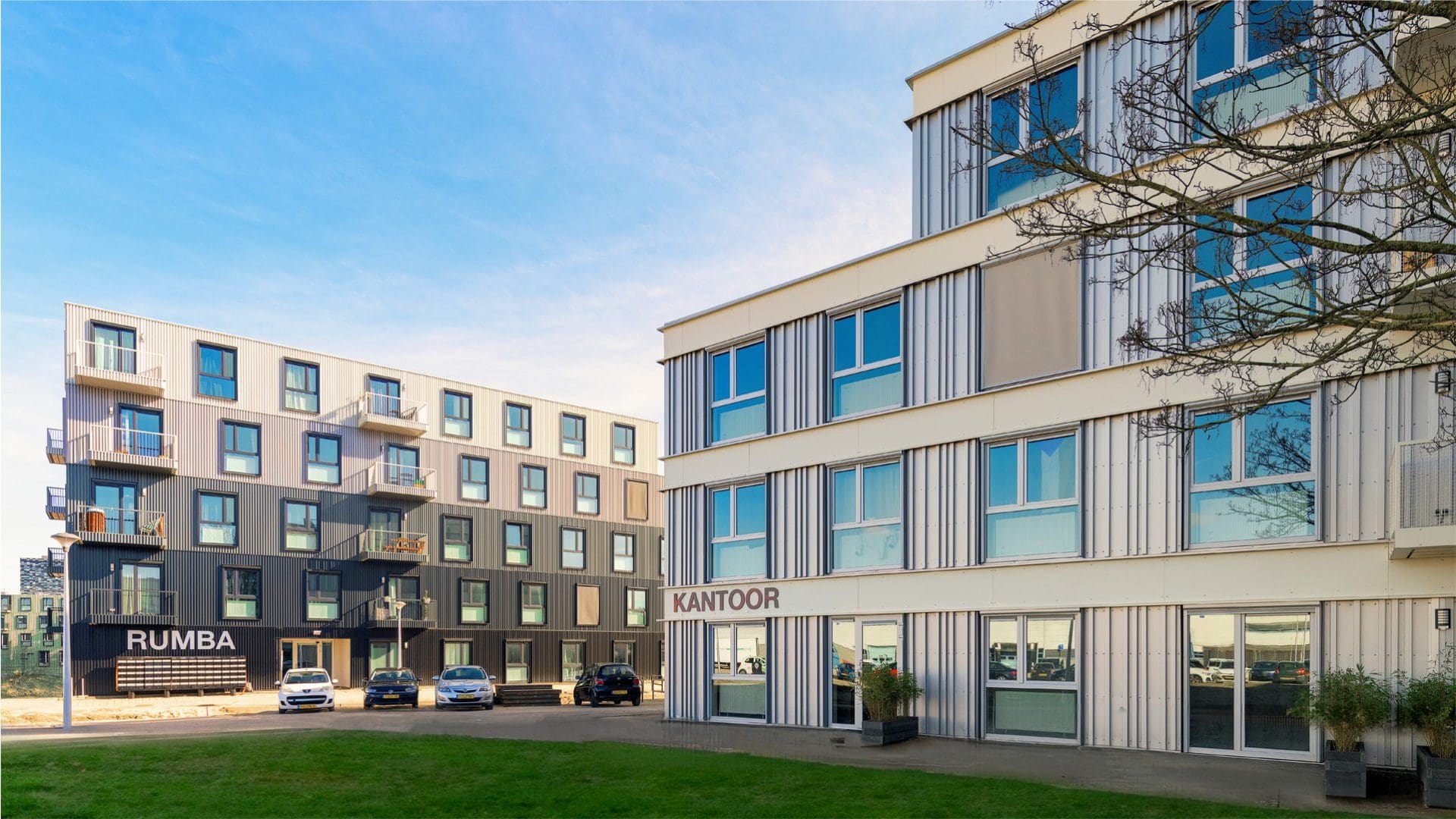
A new district in Nijmegen with roughly 500 homes, completed within 3 years.
Product mindset
A product mindset is at the heart of what VDL De Meeuw does. Van Rijt: “When we build a residential property, we think about all the requirements the property has to meet in advance as well as how we’re going to create it. In this respect, the property consists of different modules. These can be assembled according to the specific requirements of a specific customer for a specific project. Collaboration with the customer is key here. Our main focus is discussing what the customer needs. Based on those discussions, we then use the modules we have to configure the residential buildings the customer needs.”
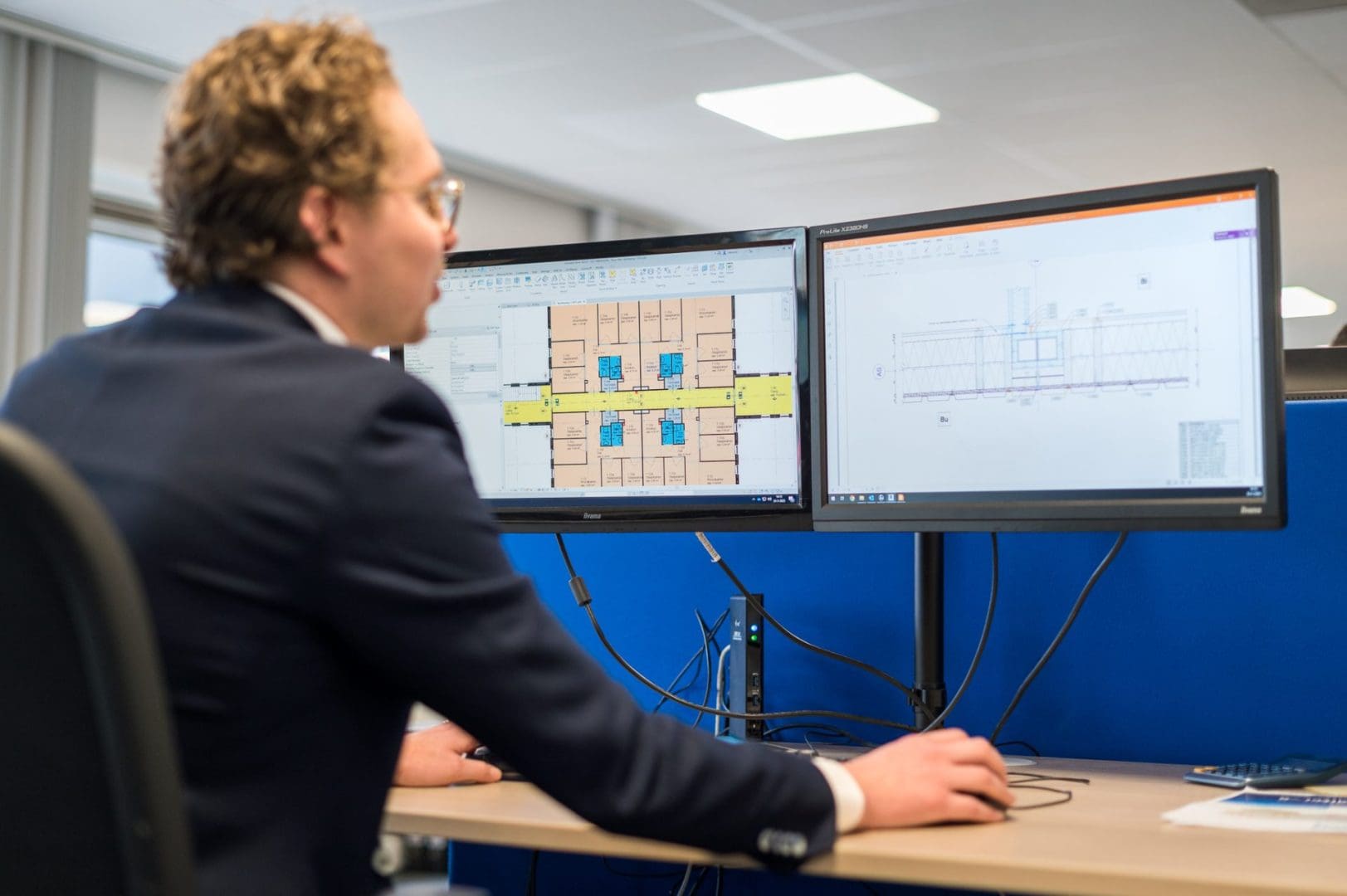
These discussions address very different topics than are covered in traditional talks, says Van de Linde. “In the past, customers would ask about what kind of tap they were going to have in their flat. But when you live somewhere, that particular tap isn’t what’s on your mind all day. You think about whether the environment you live in is nice and if your home is comfortable. Then you’re talking about the KPIs of living.”
Additional costs
At its factory in Oirschot, VDL De Meeuw is able to produce five hundred square metres of modular building material per day. That’s about twelve flats.
This process cuts construction time in half and it also saves a considerable amount of planning time. Van de Linde: “Construction always comes with additional costs. Costs for engineers, structural engineers and architects. Our way of working means that we have already incurred all those extra costs in designing the ready-made modules. In other words, you can skip the entire phase of designing a customised building. We make our configurator available to architects here, for example. They can use our building blocks to create their own designs and buildings, without the need for a structural engineer. Then we can produce the building after that.”
Van de Linde emphasised that appearance and quality are key considerations in the modular building system. A group of architects were involved in the design of the modules. “This kind of collaboration involves things like: can you create enough plasticity in cladding? Or: can you create different access solutions in a house? This approach helps us achieve a high-quality living experience.”
A feel for customisation
Modular construction is increasingly finding its way into the construction sector for permanent housing solutions. Van de Linde: “Initially, we were very much in demand for building temporary accommodation. The living experience was not considered as important in that case. But after 15 years of living opposite container flats, there is no more talk of temporary. We believe our modules are so smart that you can create a standard product that feels customised. It is definitely not a one-size-fits-all solution.”
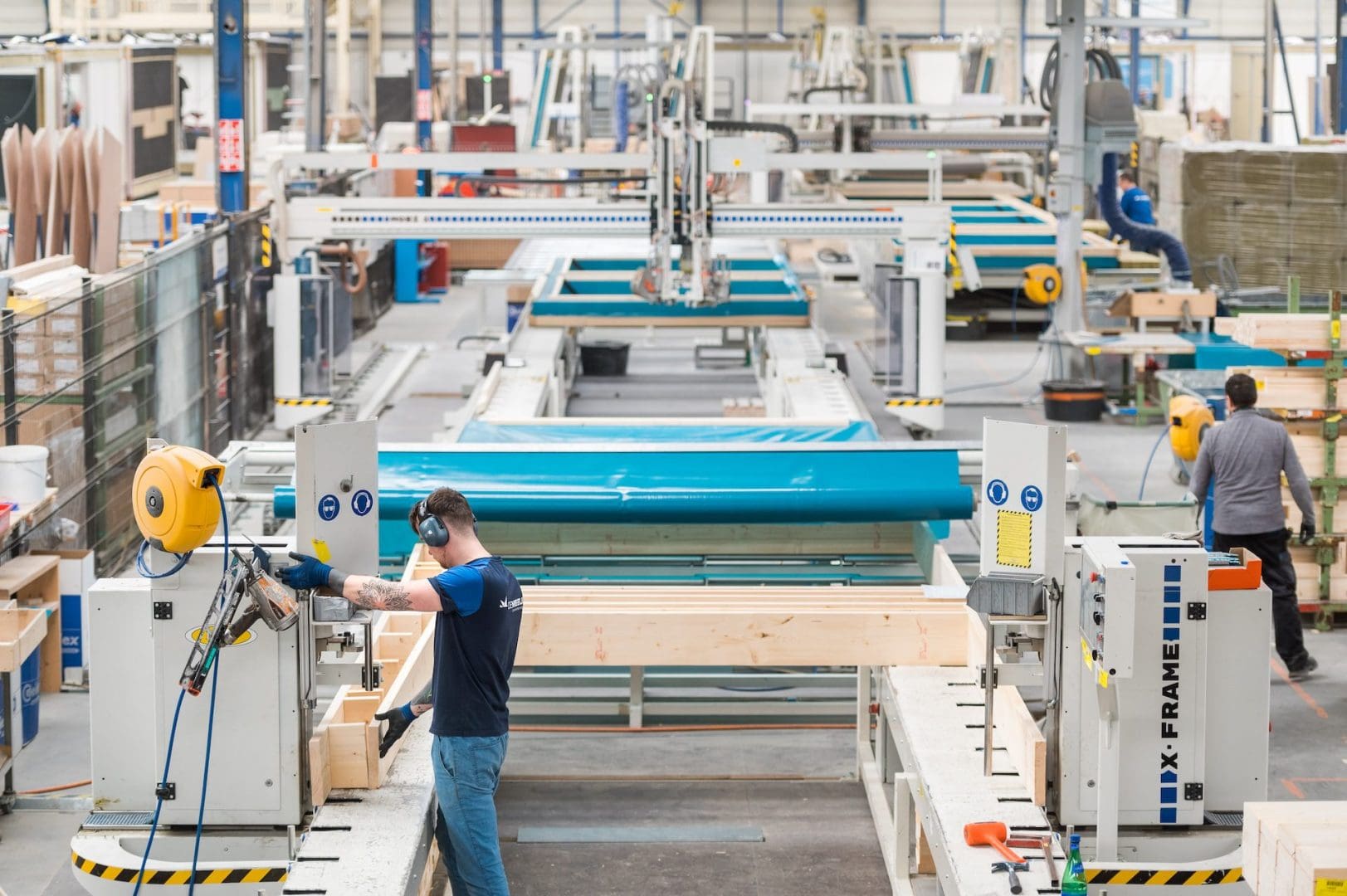
Stacking modules
Once a house has been configured and produced in the factory, it can be installed. According to Van Rijt, this installation or assembly process is like building a house out of legos. “At the construction site, it’s a matter of stacking the different modules on top of each other. A fitter will then come along and neatly finish the façade and connect the installations. Then we’re on our way again. This eliminates a lot of hassle because you have much more control at the factory. At the construction site, the size of a project is always a headache. Maybe something has been forgotten or not well thought through. The bigger a building gets, the longer the finishing process takes. We completed seven blocks of flats in Nijmegen earlier this year. Each block consisted of seventy to eighty flats. We spent about eight weeks on each block for the finishing process. That is absolutely impossible with traditional construction methods.”
Modular housing is not only interesting for temporary housing and outdoor locations, notes Van de Linde. “Our way of building is incredibly interesting for locations in city centres. Before you know it, we’re already finished. We don’t have to cordon off half the city centre and there’s also only a limited amount of truck traffic coming and going. It’s a hugely efficient way of building. That results in a very low NOx footprint. As much as 75% lower. So for complex locations in city centres, modular construction is definitely a good solution as well.”
At its factory in Oirschot, VDL De Meeuw is able to produce five hundred square metres of modular building material per day. That’s about twelve flats. This process cuts construction time in half and it also saves a considerable amount of planning time. Van de Linde: “Construction always comes with additional costs. Costs for engineers, structural engineers and architects. Our way of working means that we have already incurred all those extra costs in designing the ready-made modules. In other words, you can skip the entire phase of designing a customised building. We make our configurator available to architects here, for example. They can use our building blocks to create their own designs and buildings, without the need for a structural engineer. Then we can produce the building after that.”
Van de Linde emphasised that appearance and quality are key considerations in the modular building system. A group of architects were involved in the design of the modules. “This kind of collaboration involves things like: can you create enough plasticity in the cladding? Or: can you create different access solutions in a house? This approach helps us achieve a high-quality living experience.”